完全防水を追求した私たちレインウェア業界(以下私たち)は、生地目からの染み出しを防ぐための防水加工が施された生地を糸ミシンで縫製した後、更にその「縫い目」の部分に裏側より漏水を防ぐための「防水テープ」が貼られています。
この防水布とテープシールが、防水性を重んじる私たちが生産するレインウエアの大きな特長で、そこには長年培ったノウハウが潜んでいます。
今回はこの生地に使われている防水布とその素材に合わせたテープシールの加工法について、これまでの変革をお話してみます。
防水布のこれまでの変革
まずは防水布の変革についてのお話です。
防水布とは、織物である基布とその裏面に施す樹脂との組み合わせで成り立っています。その裏面に施す樹脂とその加工方法次第で、防水性のレベルは大きく変化します。
防水布の基布(表素材)
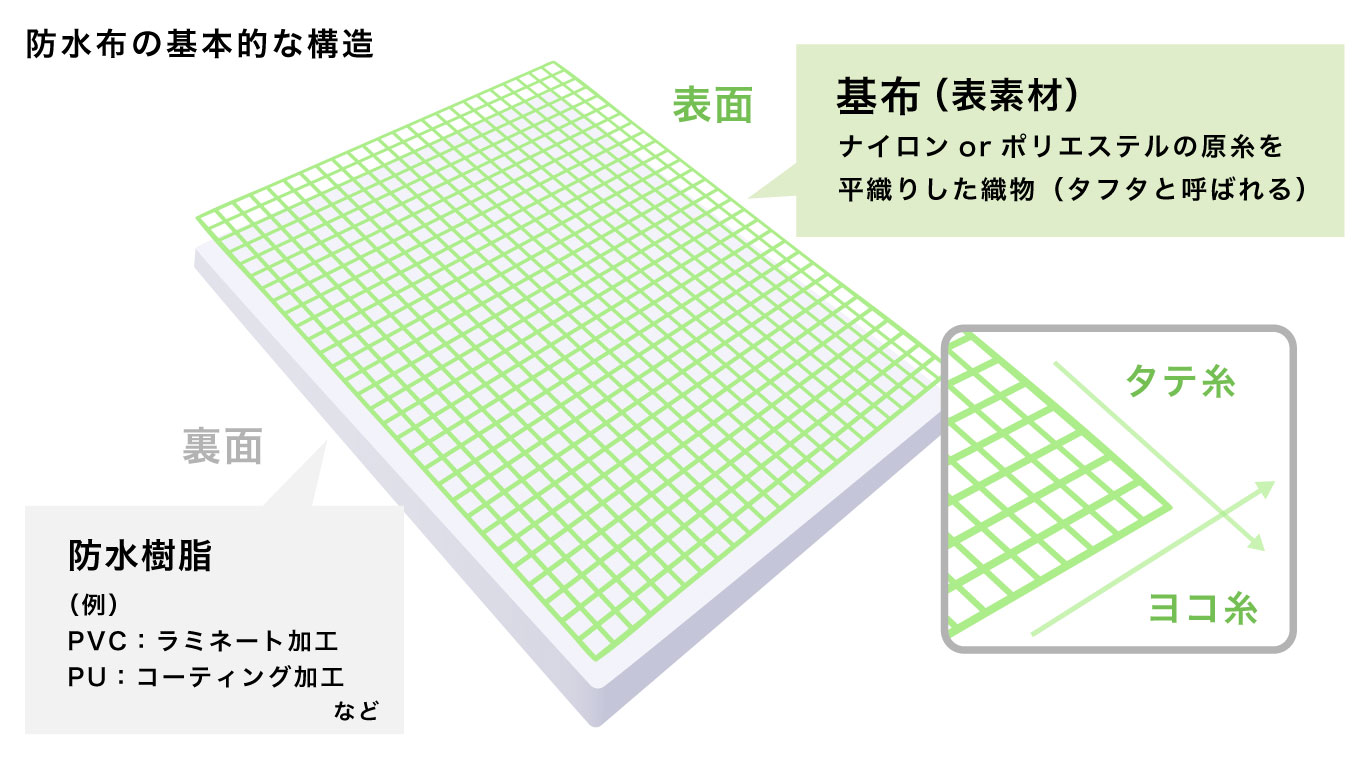
基布に使われている基本的な原糸は「ナイロン」、あるいは「ポリエステル」の2種類で、その原糸の織り方は、圧倒的にタフタと呼ばれる縦糸と横糸が1本づつ交互に交差した「平織り」です。その織物が解れないよう、まず織物の裏面に「のり引き」加工を施し安定させ、次に「染色」をしたものが、私たちが防水布の表素材にしている「基布」と表現されるものです。
余談ですが、昨今安価なレインウエアが出回り、表素材に使用されている原糸は、かつては当たり前だったナイロンに代わり、安価なポリエステルが多く見られますが、ポリエステルは摩擦摩耗に弱く、色移行(衣料の色が他の部分に移る現象)が発生する恐れがありますので、トキワでは一切使用しておりません。
話は戻ります。その基布の裏面に防水樹脂を施す事によって、防水性が高まります。
防水樹脂の加工(裏面)
防水樹脂の主原料は、そのルーツであった合成ゴムから変化して、PVC(ポリ塩化ビニル)、PU(ポリウレタン)の2種類が現在の主流です。
その加工方法はPVCの場合はラミネート加工(別々に生産した基布と樹脂を貼り合わせる)、PUの場合にはコーティング加工(基布に樹脂を付着させて覆う)です。
では、それぞれの長所を比較してみると、PVCラミネート加工の方は防水性があり、摩擦摩耗に強く、強度があります。一方、PUコーティング加工の方は軽量で耐候性があります。それぞれの短所はその逆を考えてください。つまり一長一短で、使用目的からそれらの素材を使用したレインウエアの選択をお薦めします。トキワがレインウエアに使用するこれらの防水布は、皆さんが平素使用する一般的な雨傘やウインドブレーカーに使われている生地の20倍から50倍もの防水性があります。
快適な着心地のための「透湿防水加工」
しかしこれらの防水布にも長年の課題がありました。それは、防水布は雨を通さない特徴を持っているがゆえに、逆に生地の内側の汗などを外へ逃さないため、湿気がこもり蒸れを生じます。その不快さを解消する為に進化した加工が透湿防水加工であり、水を通さないことに特化した防水加工に対して、より快適な着心地を実現する為に液体である水が通ることを防ぎつつ、気体になった湿気だけは通すという非常に高度な加工技術です。
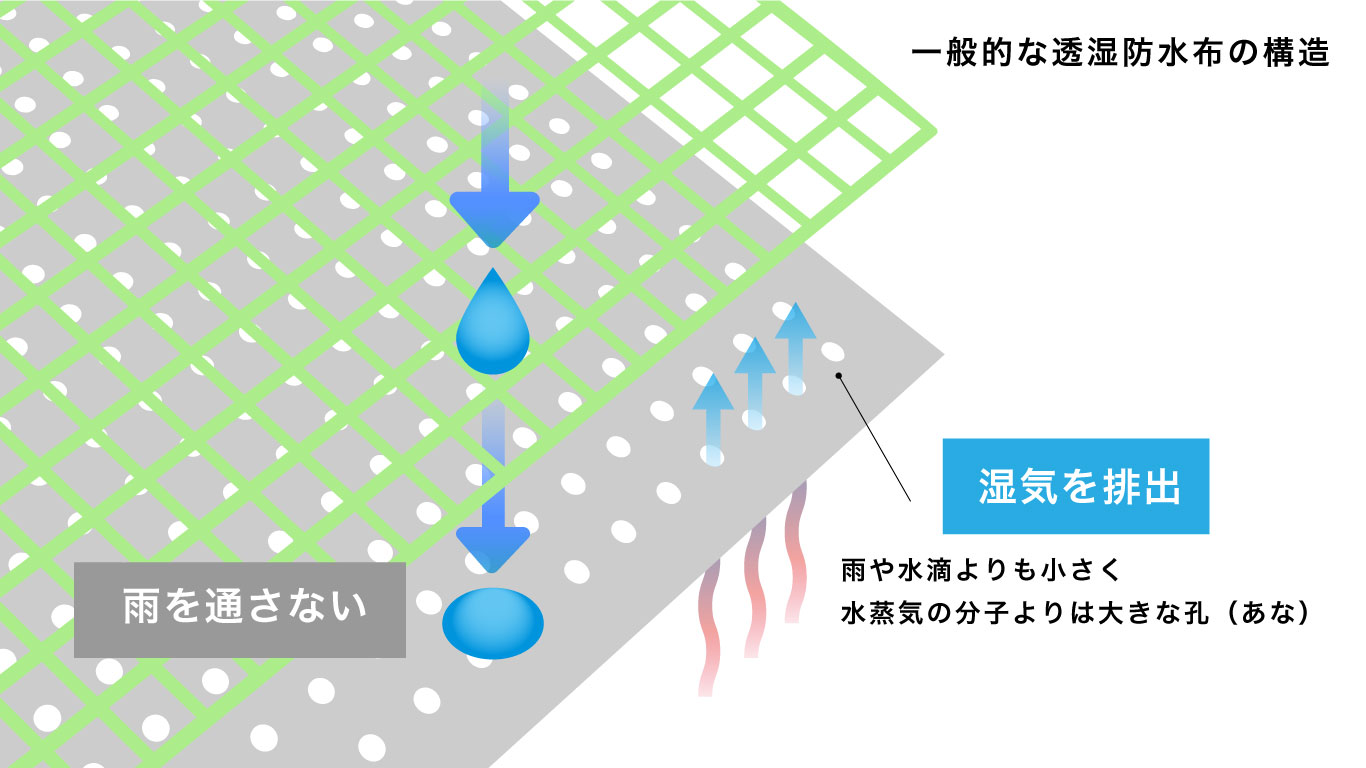
この高度な機能をどのように発揮するかというと、雨や水滴よりも小さく、水蒸気の分子よりは大きな孔(あな)が開いた特殊な被膜やフィルムを用いることが一般的です。防水と透湿を組み合わせることで雨など水の侵入を防ぎつつ、水蒸気を外へ排出することで生地内の蒸れを防ぎます。
ポリウレタン樹脂に水溶性の有機化合物を混ぜて生地面にコーティングした後に、水洗槽を通すことで有機化合物を溶かし気体通過できる微多孔(びたこう)状の被膜を生成します。
これが生地の裏面に透湿ポリウレタン樹脂をコーテイングした2層といわれる一般的な透湿防水布です。
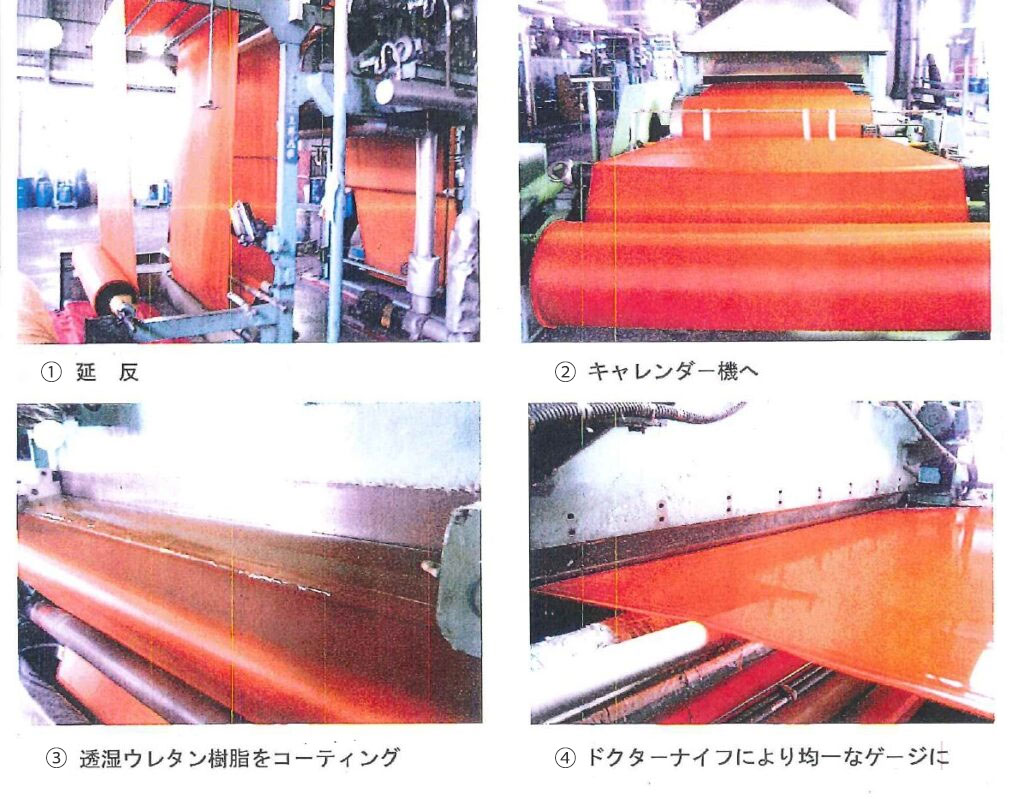
もう一つはフィルムを用いた透湿防水布で、そのフィルムを製造する場合も基本的には同じ理屈ですが、透湿フィルムには無孔質(むこうしつ)のタイプも存在します。透湿性は多孔質フィルムの方が高くなりますが、防水性は無孔質フィルムの方が高くなります。
これらのフィルムを2層(前述)の透湿防水布にラミネート加工をしたのが3層といわれる透湿防水布で、2層の被膜に使われるポリウレタン樹脂の摩擦摩耗の弱点を補うこともできます。
防水性と透湿性は反比例関係にあり、どちらを優先させるかはその使用目的に合せて選択された方が良いと思います。又、この透湿性は、防水性と同じように数値で表すことも出来ますが、透湿の度合いは防水性とは異なり、体感にかなりの個人差があり、加えて発汗にも個人差があるので、その効果を論じることは、かなり困難です。
こうして、表に使われている基布の裏面に防水樹脂を加工したものが、私たちがレインウエアに使用する「防水布」で、その防水性は前述のように一般的な雨傘やウインドブレーカーに使われている生地の20倍から50倍の生地なのです。
テープシール加工方法の変革
次にテープシールの加工方法の変革についてのお話です。
防水布の基布や防水樹脂の種類、加工方法、更にその特徴についての詳細は別にまとめた「レインウエアの知識と歴史」で記述しておりますので、ここでは割愛させていただきます。尚、ここでいう防水テープと、「シームテープ」、「目止めテープ」、「目貼りテープ」などと表現されているものは、みな同じものです。
(1)ゴム引布とテープシールの誕生
1950年代の昭和中期から長い間使われた「手貼のゴム合羽」と「ギャバ合羽」。その「手貼りのゴム合羽」は綿布の片面にゴムを引いた防水布で、「ギャバ合羽」は、スフ糸を綾織にした密度の高い基布の片面にやはりゴムを引いた防水布です。共に布にゴムを貼り合わせるという、布とゴムの特性を併せ持った複合素材で、布にゴムを貼り合わせた「ゴム引布」が合羽の素材として世の中に流通された始まりです。又、この2つの合羽が、防水テープを施した「テープシール」の始まりでもあります。
当時の防水テープは、合羽本体に使われている生地(共生地)をそのまま利用。原反の段階で約20mm幅の輪切り状に断裁したものがその原形です。合羽本体の裏側の縫い目にゴム糊を付着させたこのテープを貼り合わせますが、その作業はハンドローラーを転がしながらテープを押えて接着するという手作業で、大変手間のかかる加工法でした。
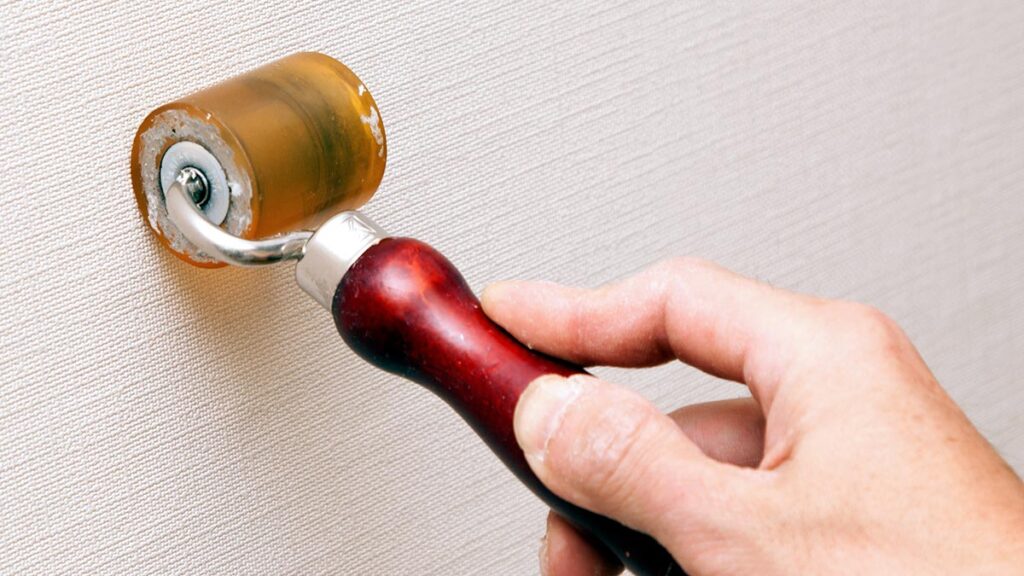
(2) 熱感テープをコテアイロンや特注ミシンで溶着
この基布にゴムを貼り合わせた防水複合素材は、その後どんどん進化していきます。
防水樹脂の主原料がゴムという事からゴムメーカーが当時の合羽の原反を生産していました。タイヤメーカーの「東京トーヨーゴム(後の東洋ゴム工業)」、ゴム長靴を製造する「興国化学工業(後のアキレス)」、スキンの「日本理研ゴム(後のオカモト)」らです。
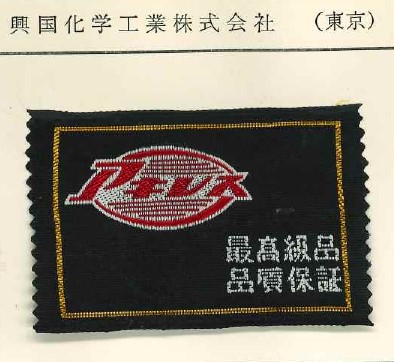
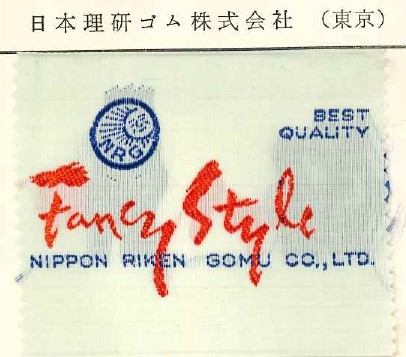
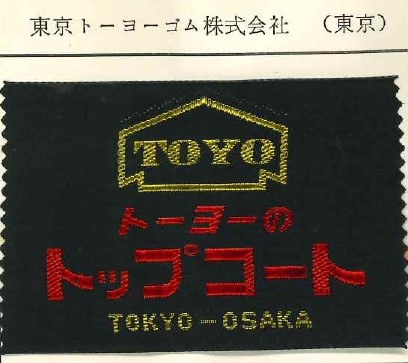
この時代にゴムメーカーと関わっていた事から、長い間レインウェア(合羽)業界は「ゴム業界」に括られていました。これらのゴムメーカーは、表に使われたナイロン基布の裏面に貼り合わせるゴムを主原料にした合成樹脂の配合やその製法を研究。高度な防水性を保ちながら「軽い」、「薄い」、「無臭」がメーカーの目指す開発テーマでした。そしてその樹脂面に貼る接着度の良い防水テープも合わせて開発します。テープを貼る事によって合羽本体の表の風合いを損なう事のないように接着性と共に薄さを重んじ、ポリエステル生地の片面に乾燥した糊をあらかじめ付着させ、熱を加えるとその糊が溶けて接着するという「熱感テープ」が誕生しました。
ただ当初はこのテープを貼る作業はやはり手作業で、約180度の熱を加えた「コテアイロン」をテープの上から押えて溶着していました。そこでこの手間を省くために、ミシンメーカーが開発したのが「熱感テープ貼りミシン」です。上下に設置された幅約50mmの2つの鉄製のローラーに熱を加え、その間に生地とテープを同時に挟んで溶着します。このミシンは特注で、1960年代後半に開発され、当時1台約100万円。このミシンによって、生産能率は著しく高まり、製品の量産が進みました。
このゴム引布の後に、軽量感、しなやかさ、無臭、耐候性の良さを売りものにしたポリウレタン樹脂を貼り合わせた防水布も誕生しましたが、テープシールの方法はゴム引布と同じ熱感式でした。しかしこの熱感テープには、度々起こる問題がありました。それは「テープはく離」、つまりテープの剥がれです。
貼る工程で、融点(接着温度)が低かったり、空気が入ったりして、テープがしっかりと貼られていないと、そこから剥がれてきます。又 テープが始めからミシン目に乗っていないといった初歩的な問題も時に見られ、漏水クレームは後を絶たず長年に亘る業界が抱える最大の課題でした。
(3)ゴム引布からビニール引布への移行と高周波ウエルダーによるテープシール
この業界最大の難問を解決した防水布とテープシールの加工方法が誕生しました。
熱感ミシンによるテープの溶着加工のはく離問題は、一向に改善が見られないまま10年以上歳月が経過、そこで糸ミシンは使わないビニール合羽の完全防水の加工法にヒントを得た高周波ウエルダーによる防水布とテープの溶着加工が始まります。これまで基布の裏面に施されていた防水樹脂の主原料であるゴムに代わり、ポリ塩化ビニル(PVC・以下塩ビ)を主原料にした引布が使用されました。
その理由は、防水テープを塩ビ製にすることで、高周波ウエルダーでの加工が可能(高周波ウエルダーの溶着加工は塩ビ同士が基本条件)になるからで、それ以降テープのはく離問題も耳にしなくなりました。
この塩ビを貼り合わせた防水布は現在でも主流の素材です。これまでは前出のゴムメーカーが私たちの原反製造元でしたが、ここで一気に塩ビメーカーが主導権を握ります。国内生産がまだ主流の1980年代でしたが、この加工をする為には、糸ミシンと高周波ウエルダーを併用するので、その両方の設備と技術者が必要になる事から国内でもその生産工場は限られていました。そのようなこともあり、生産を国内から海外(台湾)へシフトさせ、輸入品に依存する業者がどんどん増えていきます。それが安価な塩ビ引布のレインウエアが一気に増えた要因でもありました。
ただ、当時の高周波ウエルダーで目止めを施したレインウエアにも問題点はありました。
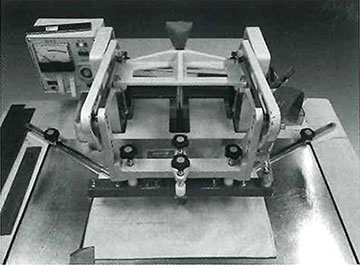
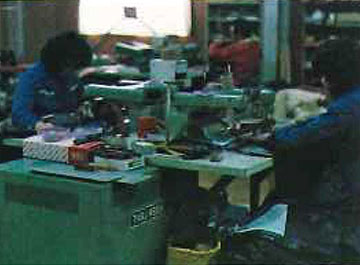
それは、高周波ウエルダーはバー(金型)をウエルダーミシンに設置、そこへ高周波を送り、塩ビと塩ビ、つまりレインウエア本体の裏側の塩ビの樹脂面に塩ビの防水テープを溶着させるのですが、金型が大きい場合には、構造上目止めが必要とされる箇所に金型が入らない事があったり、目止めの箇所の形に見合う金型の手持ちがなかったりという問題があります。新たな金型を作製しようにも金型は高額な事から、採算性の問題も生じてきます。又、テープを貼る部分イコール縫製部分、それは裁断の形にも準じますので、製品のデザインそのものにも拘束が余儀なくされるという問題点もありました。
※ 高周波ウエルダー目止め加工の前に「超音波ミシン」(超音波により防水布と防水テープを貼る)の時代が若干ありましたが、限られたごく一部の業者が短期間の使用だったので、ここでは割愛します。
雨の日に大方の人が使用する雨具、それは「傘」。しかし私たちの製品の生地は、その傘に使われている生地の50倍もの防水性を持つ生地。しかもその生地の縫製箇所の縫い目からも、漏水しないように裏側からテープシールを施すというような、手間もかかる高度な防水性を追求して来た私たちにとって、その防水布とテープシールには、これだけの進化の歴史がありました。10数年抱えたテープのはく離による漏水問題が、塩ビの防水テープを高周波ウエルダーで溶着する事によって、ほぼ解決したものの、その高周波ウエルダーにも前述のデメリットがあり、更にそれを克服した現在の加工法が生まれました。
そこでそこへ至る推移を整理してみましょう。
高周波ウエルダーによる塩ビのテープ溶着が抱えていた問題
- 素材に使われる防水布は塩ビを貼り合わせた生地に限られる。
- R(湾曲)の部分など縫製箇所に見合う金型の手持ちが必ずしもあるわけではなく、又、その金型を新たに作る場合には、高額な費用を要する。
- 高周波ウエルダーは近隣の電波障害を起こす恐れがあるので、住宅街を外すなど、工場の立地条件に制約がある。
そこでこれらの課題をクリアした現在行われている最新のテープシールの加工法とその素材(防水布)との関係性について説明をしてみます。
(4)熱風(温風)溶着ミシンの誕生
ミシンメーカーの傑作と言われたこの新型ミシンが、「熱風(温風)ミシン」。
ミシンに設置されたエアーアーム(熱風ノズル)から噴き出す500度~600度の電熱により防水布と防水テープを貼り合わせます。
そのテープは高周波ウエルダー加工と同じ塩ビ製ですが、金型で溶着した場合とは異なり、製品本体の表の風合いを損ねず、しかもフトコロ内部のテープ溶着が可能なので、基本的にあらゆるところに防水テープを貼る事が実現、その結果デザインもかなり斬新なものが可能、大きな進化を遂げました。
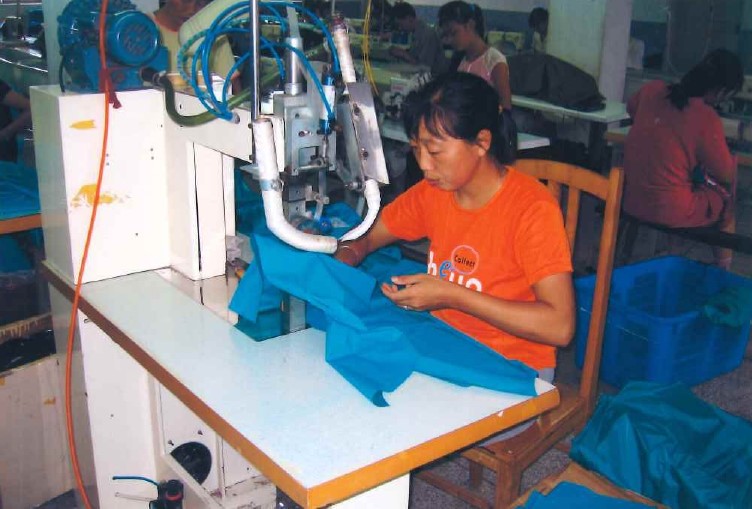
そして何よりも高周波ウエルダーの場合には塩ビの引布に限られていた防水素材が、その塩ビはもちろん、TPU、ポリウレタン等幅広い素材への対応が可能になり、しかもそれらのどの素材であっても防水テープは共通のものを使用する事が可能で、接着度も高く、このミシンの作業能率は、これまでのどのテープ貼り作業よりもスピーディで確実、更に前述のように素材とテープの関係性には優れた利便性がありました。
こうして長年に亘り、私たちが「完全防水」を追求する為に、生地の防水布とその素材に合わせたテープシールの加工法は紆余曲折あり、改良に改良を重ねてこん日があります。
この間、度重なる「テープはく離」の苦い経験をして来たトキワとしては、昨今「ストレッチ素材」なるものが表素材として使われるようになりましたが、一般衣料としては大変快適な素材だとは思いますが、レインウエアの場合、表素材が伸縮する上で、裏面に貼られた「テープシール」が、その伸縮に連動する事は間違いなく、それによって引き起こす「テープはく離」を心配しています。その不安感からトキワとしては、この素材の使用に躊躇している事を敢えて付け加えておきたいと思います。